Comprehensive foundry expertise, first-rate support
Founded in 1974, Chemex Foundry Solutions GmbH is a global technology leader, supplying foundries around the world with innovative and customised feeder systems. As a member of the HA Group, Chemex draws on the pooled expertise and resources of one of the world’s leading foundry suppliers.
Service is our number one priority
For foundries, for every challenge, for optimum all-round service: as the strongest feeder team in the world we understand our customers’ wants and needs and know how to meet them. With decades of experience in developing and manufacturing feeder systems, our experts work closely with our customers to identify the ideal system for every requirement. We offer individual consulting, state-of-the-art technology, and a broad portfolio of products that we continuously optimise and develop. Our Research & Development team is constantly testing new materials and qualifying them until they are ready for series production. At Chemex, theory and practice go hand in hand, allowing us to develop new products to support our customers quickly and efficiently in their production processes.
Simulation Service
We know the challenges our customers face: ever tighter cycle times and production schedules. And we help them stay one step ahead by using innovative simulation software to simulate the interaction of individual influencing variables in the casting process and thus optimise their processes and cut costs.
We are committed to providing our customers with the best possible service – which is why we have been offering them mould filling and solidification simulations for many years now. Our mould filling and solidification simulations are exclusively conducted using the latest software tools from our simulation partner, MAGMA, which allow us not only to evaluate the simulation results in close exchange with the on-site product management team, but also, with the help of MAGMAinteract®, to give our customers the ability to visualise and analyse the results even without their own Magmasoft® licenses.
The role of simulation software in the optimal design of feeder systems is becoming increasingly important. Therefore, Chemex has decided to further expand this business segment by establishing its own Simulation Department. This also puts us in a strong position to respond to the increasing demand from foundries for mould filling and solidification simulations.
Our simulations not only visualise the end result of the process, they also map every single stage of the filling and solidification process. This allows us to learn more about the causes of defects and gain a deeper understanding of the process in its entirety.
Would you like to find out more about our range of simulation services?
Our simulation expert Dipl.-Ing. Markus Effmert is ready and waiting to answer your questions.
More efficient processes thanks to simulation
Our team of experts would be delighted to answer your questions and talk you through the results of several simulations with different feeder positions and feeder types. The results of these simulations can then either be evaluated together with our product managers or made available and viewed in various tools.
At the same time, our team of experts is dedicated to implementing our data sets into simulation software so that our customers can independently perform simulations with our feeders. Currently, our feeder data are available in the following simulation tools:
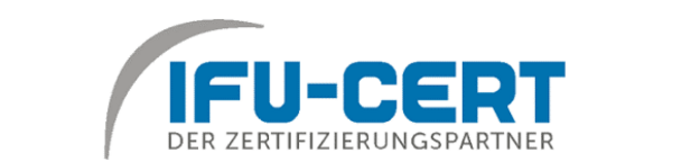
Certified quality
You can rely on the quality of our products. We are certified under the environmental management standard DIN EN ISO 14001 and constantly document our responsible and sustainable use of resources. We only use state-of-the-art core shooters, scrubbers and compressors, all of which have been continuously upgraded since 2001. We also constantly review and improve the way we safeguard and use resources.
Chemex works with a certified quality management system in compliance with the DIN EN ISO 9001 standard. The quality of our feeder systems is evaluated using a range of approaches, including thermo-physical methods. Parameters such as gas permeability and flexural strength are also systematically monitored. During exothermic testing, we also determine ignition and burning times.