Always innovating
Our research is consistently focused on developing products that deliver the best applicability and practicality – all over the world. In addition to researching new formulations and technologies in our laboratories, we also use CAD and simulation software as we continuously enhance our feeding systems. These state-of-the-art software tools are a massive aid, especially in the development of innovative feeder geometries.
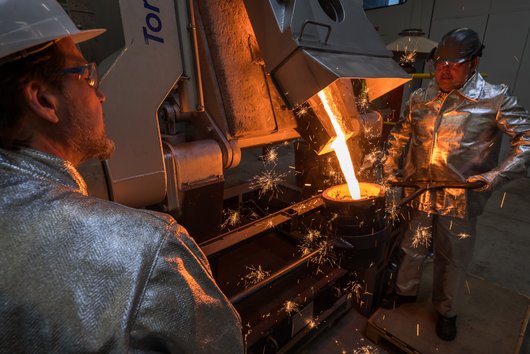
Uniting theory and practice
With the opening of the HA Center of Competence (HA CoC), the HA Group has created a truly one-of-a-kind cooperation platform for foundries, machine manufacturers, toolmakers and the entire HA Group. The idea behind the HA CoC is quite simple: Together, we can reach our goals faster. By bringing experts together at one table, we can shorten the time it takes to get from an initial idea to series production.
Thanks to partnership-based collaboration, we are able to bring products to market faster and in a more targeted manner. Best of all, our customers can immediately integrate these new products in their production processes. The HA CoC is the perfect place to test our technologies, developed in the lab and successfully simulated on the computer, in practice.
Simulation
Chemex Foundry Solutions GmbH’s new simulation department offers our customers a comprehensive package of services: Our team of experts is always available to simulate various combinations ahead of their use in production. This not only saves you time, but also reduces your costs. We focus on the implementation of new formulations and the optimisation of existing data sets, massively accelerating the development and testing of innovative solutions for foundries around the world. Contact us today!
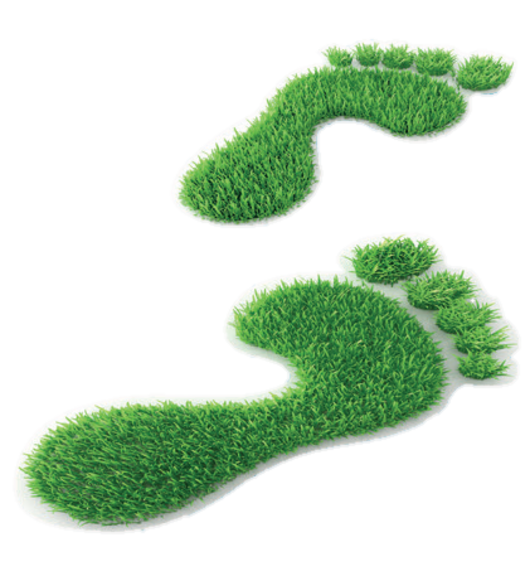
The future is green
What does this mean for the HA Group as a whole? With more efficient products and processes, we have been supporting the foundry family for decades.
Never willing to rest on our laurels, we are constantly equipping ourselves to meet the challenges of tomorrow. For example, we are:
- conducting intensive research into sustainable and environmentally-friendly binder systems
- developing innovative research methods
- collaborating with universities and institutes
- investing in sustainable production technologies
Decades ago, the HA Group recognised environmental protection as an opportunity for the foundry industry. ln this spirit, we are systematically driving advances in product development aimed at protecting the environment and mitigating climate change.
We research and develop products that help our customers reduce emissions in their manufacturing processes and keep raw materials in the material cycle. We take appropriate measures to minimise the impact of our production processes and products on the environment, both locally and more widely.
Among our innovative solutions are inorganic binder systems. With the help of inorganic binders (IOBs), our vision of emission-free casting has already become reality in our home country, Germany. And every day, demand for this technology is also growing in other parts of the world. Due to their composition, they are completely different from conventional binders based on organic chemistry.
On the path to more sustainable, low-resource processes, inorganic binders are increasingly becoming the focus of strategic decisions throughout the foundry industry.
The CSP Project
One of the key raw materials for the production of feeders are what is known as “spheres”. These are hollow ceramic spheres that are an essential component of feeder formulations. Global production is limited and, in order to reduce our dependence on the global raw materials market and to offer our customers consistent quality with the highest possible security of supply, Chemex has launched the CSP Project.
CSP stands for core-shell particles, which are used to substitute the traditional spheres in feeder formulations.
In the course of this project, Chemex has succeeded in developing a proprietary process that allows us to produce a highly heat-resistant insulating material synthetically. The aim of the CSP project is to use the newly developed process to produce the necessary qualities and quantities of CSP at our Delligsen site. To begin with, insulating formulations are currently being converted to synthetically produced CSPs.